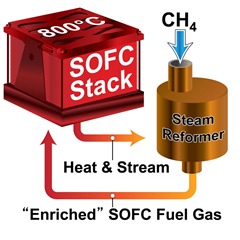
Individual homes and entire neighborhoods could be powered with a new, small-scale solid oxide fuel cell system that achieves up to 57 percent efficiency, significantly higher than the 30 to 50 percent efficiencies previously reported for other solid oxide fuel cell systems of its size, according to a study published in this month’s issue of Journal of Power Sources.
The smaller system, developed at the Department of Energy’s Pacific Northwest National Laboratory, uses methane, the primary component of natural gas, as its fuel. The entire system was streamlined to make it more efficient and scalable by using PNNL-developed microchannel technology in combination with processes called external steam reforming and fuel recycling. PNNL’s system includes fuel cell stacks developed earlier with the support of DOE’s Solid State Energy Conversion Alliance.
“Solid oxide fuels cells are a promising technology for providing clean, efficient energy. But, until now, most people have focused on larger systems that produce 1 megawatt of power or more and can replace traditional power plants,” said Vincent Sprenkle, a co-author on the paper and chief engineer of PNNL’s solid oxide fuel cell development program. “However, this research shows that smaller solid oxide fuel cells that generate between 1 and 100 kilowatts of power are a viable option for highly efficient, localized power generation.”
Sprenkle and his co-authors had community-sized power generation in mind when they started working on their solid oxide fuel cell, also known as a SOFC. The pilot system they built generates about 2 kW of electricity, or how much power a typical American home consumes. The PNNL team designed its system so it can be scaled up to produce between 100 and 250 kW, which could provide power for about 50 to 100 American homes.
Goal: Small and efficient
Knowing the advantages of smaller SOFC systems (see the “What is an SOFC?” sidebar below for more information), the PNNL team wanted to design a small system that could be both more than 50 percent efficient and easily scaled up for distributed generation. To do this, the team first used a process called external steam reforming. In general, steam reforming mixes steam with the fuel, leading the two to react and create intermediate products. The intermediates, carbon monoxide and hydrogen, then react with oxygen at the fuel cell’s anode. Just as described in the below sidebar, this reaction generates electricity, as well as the byproducts steam and carbon dioxide.
Steam reforming has been used with fuel cells before, but the approach requires heat that, when directly exposed to the fuel cell, causes uneven temperatures on the ceramic layers that can potentially weaken and break the fuel cell. So the PNNL team opted forexternal steam reforming, which completes the initial reactions between steam and the fuel outside of the fuel cell.
The external steam reforming process requires a device called a heat exchanger, where a wall made of a conductive material like metal separates two gases. On one side of the wall is the hot exhaust that is expelled as a byproduct of the reaction inside the fuel cell. On the other side is a cooler gas that is heading toward the fuel cell. Heat moves from the hot gas, through the wall and into the cool incoming gas, warming it to the temperatures needed for the reaction to take place inside the fuel cell.
Efficiency with micro technology
The key to the efficiency of this small SOFC system is the use of a PNNL-developed microchannel technology in the system’s multiple heat exchangers. Instead of having just one wall that separates the two gases, PNNL’s microchannel heat exchangers have multiple walls created by a series of tiny looping channels that are narrower than a paper clip. This increases the surface area, allowing more heat to be transferred and making the system more efficient. PNNL’s microchannel heat exchanger was designed so that very little additional pressure is needed to move the gas through the turns and curves of the looping channels.
The second unique aspect of the system is that it recycles. Specifically, the system uses the exhaust, made up of steam and heat byproducts, coming from the anode to maintain the steam reforming process. This recycling means the system doesn’t need an electric device that heats water to create steam. Reusing the steam, which is mixed with fuel, also means the system is able to use up some of the leftover fuel it wasn’t able to consume when the fuel first moved through the fuel cell.
The combination of external steam reforming and steam recycling with the PNNL-developed microchannel heat exchangers made the team’s small SOFC system extremely efficient. Together, these characteristics help the system use as little energy as possible and allows more net electricity to be produced in the end. Lab tests showed the system’s net efficiency ranged from 48.2 percent at 2.2 kW to a high of 56.6 percent at 1.7 kW. The team calculates they could raise the system’s efficiency to 60 percent with a few more adjustments.
The PNNL team would like to see their research translated into an SOFC power system that’s used by individual homeowners or utilities.
“There still are significant efforts required to reduce the overall cost to a point where it is economical for distributed generation applications,” Sprenkle explained. “However, this demonstration does provide an excellent blueprint on how to build a system that could increase electricity generation while reducing carbon emissions.”