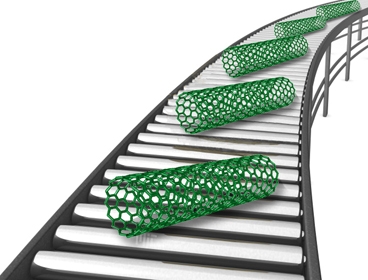
Study suggests new way for manufacturers to minimize environmental impact of carbon nanotube production
Given their size, strength and electrical properties, carbon nanotubes — tiny, hollow cylinders made of carbon atoms — hold promise for a range of applications in electronics, medicine and other fields. Despite industrial development of nanotubes in recent years, however, very little is known about how they form or the environmental impacts of their manufacture.
It turns out that one process commonly used to produce carbon nanotubes, or CNTs, may release several hundred tons of chemicals, including greenhouse gases and hazardous air pollutants, into the air each year. In a paper published last week on the ACS Nano website, the researchers report that in experiments, removing one step in that process — a step that involves heating carbon-based gases and adding key reactive “ingredients” — reduced emissions of harmful by-products at least tenfold and, in some cases, by a factor of 100. It also cut the amount of energy used in the process by half.
“We were able to do all of this and still have good CNT growth,” says Desiree Plata, who led the research between 2007 and 2009 as a doctoral student in MIT’s joint program with the Woods Hole Oceanographic Institution. Now a visiting assistant professor in MIT’s Departments of Aeronautics and Astronautics and Civil and Environmental Engineering (CEE), Plata collaborated on the paper with several MIT and University of Michigan researchers, including Philip Gschwend, Ford Professor of Engineering in CEE, and John Hart, a mechanical engineering professor at the University of Michigan. The study is part of a long-term effort to change the approach to material development so that environmental chemists work with the young CNT industry to develop methods to prevent or limit undesirable environmental consequences.
In their study, Plata and her colleagues analyzed a common CNT manufacturing process known as catalytic chemical vapor deposition. In this method, manufacturers combine hydrogen with a “feedstock gas,” such as methane, carbon monoxide or ethylene. They then heat the combination in a reactor that contains a metal catalyst like nickel or iron, which then forms CNTs. The problem is that once the CNTs form, unreacted compounds (up to 97 percent of the initial feedstock) are often released into the air.
Turning off the heat
In a custom-made laboratory-scale reactor, the researchers heated hydrogen and ethylene, which is commonly used in high-volume CNT manufacturing, and then delivered it to a metal catalyst. They found that more than 40 compounds formed, including greenhouse gases like methane and toxic air pollutants like benzene.
The researchers suspected that not all of those compounds were essential for growing CNTs, and they knew that heating the feedstock gas plays a critical role in creating the dangerous compounds. So they combined unheated ethylene and hydrogen with several of the 40 compounds, one by one, to see which combination of compounds led to the best growth. They observed that certain alkynes, or molecules that have at least two carbon atoms stuck together with three distinct bonds, produced the best growth, while other compounds that are undesirable by-products, such as methane and benzene, did not.
Plata and her colleagues accomplished their dramatic reduction in both harmful emissions and energy consumption by impinging room-temperature alkynes, with ethylene and hydrogen, directly onto the metal catalyst, without heat. They also learned that they could reduce the amount of ethylene and hydrogen used by about 20 and 40 percent, respectively, and still achieve the same rate and quality of CNT growth. Plata says that while the results of lab experiments are hard to generalize, in a market that is expected to reach several billion dollars within several years, these changes could translate into “significant cost savings” for manufacturers.
Industry reaction
Although it’s too soon for manufacturers to adopt the method presented in the paper, David Lashmore, vice president and chief technology officer of Concord, N.H.-based Nanocomp Technologies, says the method is something his company is willing to try as it looks for ways to minimize the environmental effects of its production process. “This is of high interest to us and could have a broad impact on our process economics,” he says.
Plata points out that the MIT study analyzed only one of several feedstock gases used to make CNTs, and that the same analysis needs to be done for the others. But for her own part, she is now focusing on how CNTs form, trying to determine the precise interaction of the metal catalyst and the hydrocarbons in this process. Knowing the catalyst’s role could help researchers manipulate CNTs’ formation atom by atom — much more precisely than they can now, she says.
The study was funded by the Woods Hole Oceanographic Institution, the Arunas and Pam Chesonis Ignition Grant via the MIT Earth Systems Initiative and the MIT Martin Society of Fellows for Sustainability, the Nanomanufacturing Program of the National Science Foundation, Lockheed Martin Nanosystems and the University of Michigan Department of Mechanical Engineering and College of Engineering.