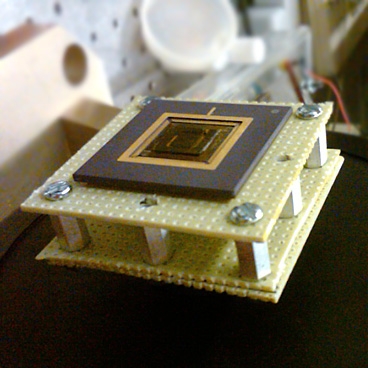
Today’s wireless-sensor networks can do everything from supervising factory machinery to tracking environmental pollution to measuring the movement of buildings and bridges.
Working together, distributed sensors can monitor activity along an oil pipeline or throughout a forest, keeping track of multiple variables at a time.
While uses for wireless sensors are seemingly endless, there is one limiting factor to the technology — power. Even though improvements have brought their energy consumption down, wireless sensors’ batteries still need changing periodically. Especially for networks in remote locales, replacing batteries in thousands of sensors is a staggering task.
To get around the power constraint, researchers are harnessing electricity from low-power sources in the environment, such as vibrations from swaying bridges, humming machinery and rumbling foot traffic. Such natural energy sources could do away with the need for batteries, powering wireless sensors indefinitely.
Now researchers at MIT have designed a device the size of a U.S. quarter that harvests energy from low-frequency vibrations, such as those that might be felt along a pipeline or bridge. The tiny energy harvester — known technically as a microelectromechanical system, or MEMS — picks up a wider range of vibrations than current designs, and is able to generate 100 times the power of devices of similar size.
“There are wireless sensors widely available, but there is no supportive power package,” says Sang-Gook Kim, a professor of mechanical engineering at MIT . “I think our vibrational-energy harvesters are a solution for that.”
To harvest electricity from environmental vibrations, researchers have typically looked to piezoelectric materials such as quartz and other crystals. Such materials naturally accumulate electric charge in response to mechanical stress (piezo, in Greek, means to squeeze or press). In the past few years, researchers have exploited piezoelectric material, at the microscale, engineering MEMS devices that generate small amounts of power.
Various groups have gravitated toward a common energy-harvesting design: a small microchip with layers of piezoelectric material glued to the top of a tiny cantilever beam. As the chip is exposed to vibrations, the beam moves up and down like a wobbly diving board, bending and stressing the piezoelectric material layers. The stressed material builds up an electric charge, which can be picked up by arrays of tiny electrodes.
Kim and Hajati came up with a design that increases the device’s frequency range, or bandwidth, while maximizing the power density, or energy generated per square centimeter of the chip. Instead of taking a cantilever-based approach, the team went a slightly different route, engineering a microchip with a small bridge-like structure that’s anchored to the chip at both ends. The researchers deposited a single layer of piezoelectric material to the bridge, placing a small weight in the middle of it.
The team then put the device through a series of vibration tests, and found it was able to respond not just at one specific frequency, but also at a wide range of other low frequencies. The researchers calculated that the device was able to generate 45 microwatts of power with just a single layer of piezoelectric material — an improvement of two orders of magnitude compared to current designs.
Hajati says the team plans to do just that, optimizing the design to respond to lower frequencies and generate more power.
“Our target is at least 100 microwatts, and that’s what all the electronics guys are asking us to get to,” says Hajati, now a MEMS development engineer at FujiFilm Dimatix in Santa Clara, Calif. “For monitoring a pipeline, if you generate 100 microwatts, you can power a network of smart sensors that can talk forever with each other, using this system.”