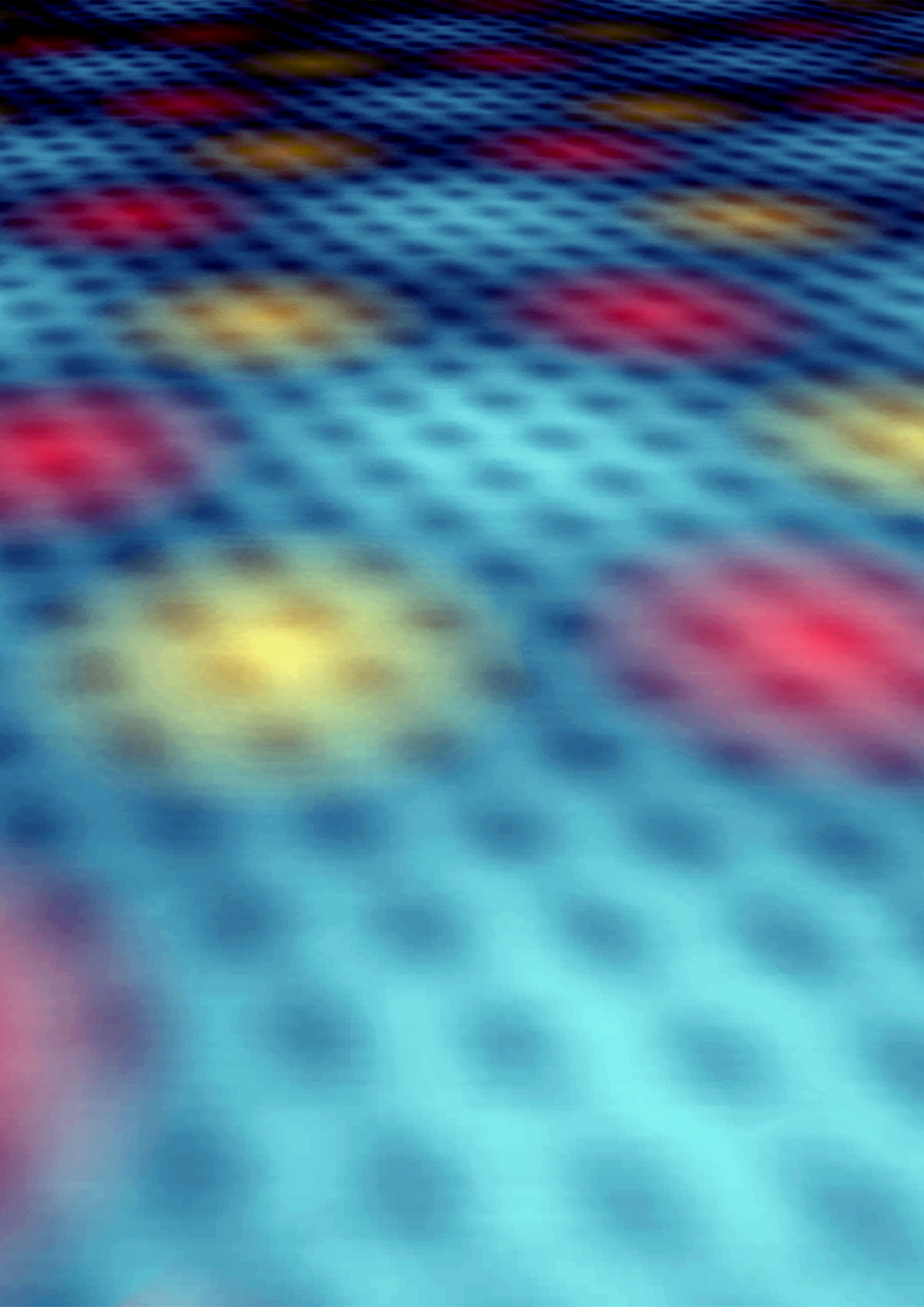
That material, the focus of the 2010 Nobel Prize in physics, is graphene – a fancy name for extremely thin layers of ordinary carbon atoms arranged in a “chicken-wire” lattice. These layers, sometimes just a single atom thick, conduct electricity with virtually no resistance, very little heat generation – and less power consumption than silicon.
With silicon device fabrication approaching its physical limits, many researchers believe graphene can provide a new platform material that would allow the semiconductor industry to continue its march toward ever-smaller and faster electronic devices – progress described in Moore’s Law. Though graphene will likely never replace silicon for everyday electronic applications, it could take over as the material of choice for high-performance devices.
And graphene could ultimately spawn a new generation of devices designed to take advantage of its unique properties.
Since 2001, Georgia Tech has become a world leader in developing epitaxial graphene, a specific type of graphene that can be grown on large wafers and patterned for use in electronics manufacturing. In a recent paper published in the journal Nature Nanotechnology, Georgia Tech researchers reported fabricating an array of 10,000 top-gated transistors on a 0.24 square centimeter chip, an achievement believed to be the highest density reported so far in graphene devices.
In creating that array, they also demonstrated a clever new approach for growing complex graphene patterns on templates etched into silicon carbide. The new technique offered the solution to one of the most difficult issues that had been facing graphene electronics.
“This is a significant step toward electronics manufacturing with graphene,” said Walt de Heer, a professor in Georgia Tech’s School of Physics who pioneered the development of graphene for high-performance electronics. “This is another step showing that our method of working with epitaxial graphene grown on silicon carbide is the right approach and the one that will probably be used for making graphene electronics.”
Unrolled Carbon Nanotubes
For de Heer, the story of graphene begins with carbon nanotubes, tiny cylindrical structures considered miraculous when they first began to be studied by scientists in 1991. De Heer was among the researchers excited about the properties of nanotubes, whose unique arrangement of carbon atoms gave them physical and electronic properties that scientists believed could be the foundation for a new generation of electronic devices.
Carbon nanotubes still have attractive properties, but the ability to grow them consistently – and to incorporate them in high-volume electronics applications – has so far eluded researchers. De Heer realized before others that carbon nanotubes would probably never be used for high-volume electronic devices.
But he also realized that the key to the attractive electronic properties of the nanotubes was the lattice created by the carbon atoms. Why not simply grow that lattice on a flat surface, and use fabrication techniques proven in the microelectronics industry to create devices in much the same way as silicon integrated circuits?
By heating silicon carbide – a widely-used electronic material – de Heer and his colleagues were able to drive silicon atoms from the surface, leaving just the carbon lattice in thin layers of graphene large enough to grow the kinds of electronic devices familiar to a generation of electronics designers.
That process was the basis for a patent filed in 2003, and for initial research support from chip-maker Intel. Since then, de Heer’s group has published dozens of papers and helped spawn other research groups also using epitaxial graphene for electronic devices. Though scientists are still learning about the material, companies such as IBM have launched research programs based on epitaxial graphene, and agencies such as the National Science Foundation (NSF) and Defense Advanced Research Projects Agency (DARPA) have invested in developing the material for future electronics applications.
Georgia Tech’s work on developing epitaxial graphene for manufacturing electronic devices was recognized in the background paper produced by the Royal Swedish Academy of Sciences as part of the Nobel Prize documentation.
The race to find commercial applications for graphene is intense, with researchers from the United States, Europe, Japan and Singapore engaged in well-funded efforts. Since awarding of the Nobel to a group from the United Kingdom, the flood of news releases about graphene developments has grown.
“Our epitaxial graphene is now used around the world by many research laboratories,” de Heer noted. “We are probably at the stage where silicon was in the 1950s. This is the beginning of something that is going to be very large and important.”
Silicon “Running Out of Gas”
A new electronics material is needed because silicon is running out of miniaturization room.
“Primarily, we’ve gotten the speed increases from silicon by continually shrinking feature sizes and improving interconnect technology,” said Dennis Hess, director of the National Science Foundation-sponsored Materials Research Science and Engineering Center(MRSEC) established at Georgia Tech to study future electronic materials, starting with epitaxial graphene. “We are at the point where in less than 10 years, we won’t be able to shrink feature sizes any farther because of the physics of the device operation. That means we will either have to change the type of device we make, or change the electronic material we use.”
It’s a matter of physics. At the very small size scales needed to create ever more dense device arrays, silicon generates too much resistance to electron flow, creating more heat than can be dissipated and consuming too much power.
Graphene has no such restrictions, and in fact, can provide electron mobility as much as 100 times better than silicon. De Heer believes his group has developed the roadmap for the future of high-performance electronics – and it is paved with epitaxial graphene.
“We have basically developed a whole scheme for making electronics out of graphene,” he said. “We have set down what we believe will be the ground rules for how that will work, and we have the key patents in place.”
Silicon, of course, has matured over many generations through constant research and improvement. De Heer and Hess agree that silicon will always be around, useful for low-cost consumer products such as iPods, toasters, personal computers and the like.
De Heer expects graphene to find its niche doing things that couldn’t otherwise be done.
“We’re not trying to do something cheaper or better; we’re going to do things that can’t be done at all with silicon,” he said. “Making electronic devices as small as a molecule, for instance, cannot be done with silicon, but in principle could be done with graphene. The key question is how to extend Moore’s Law in a post-CMOS world.”
Unlike the carbon nanotubes he studied in the 1990s, de Heer sees no major problems ahead for the development of epitaxial graphene.
“That graphene is going to be a major player in the electronics of the future is no longer in doubt,” he said. “We don’t see any real roadblocks ahead. There are no flashing red lights or other signs that seem to say that this won’t work. All of the issues we see relate to improving technical issues, and we know how to do that.”
Making the Best Graphene
Since beginning the exploration of graphene in 2001, de Heer and his research team have made continuous improvements in the quality of the material they produce, and those improvements have allowed them to demonstrate a number of physical properties – such as the Quantum Hall Effect – that verify the unique properties of the material.
“The properties that we see in our epitaxial graphene are similar to what we have calculated for an ideal theoretical sheet of graphene suspended in the air,” said Claire Berger, a research scientist in the Georgia Tech School of Physics who also has a faculty appointment at the Centre National de la Recherche Scientifique in France. “We see these properties in the electron transport and we see these properties in all kinds of spectroscopy. Everything that is supposed to be occurring in a single sheet of graphene we are seeing in our systems.”
Key to the material’s future, of course, is the ability to make electronic devices that work consistently. The researchers believe they have almost reached that point.
“All of the properties that epitaxial graphene needs to make it viable for electronic devices have been proven in this material,” said Ed Conrad, a professor in Georgia Tech’s School of Physics who is also a MRSEC member. “We have shown that we can make macroscopic amounts of this material, and with the devices that are scalable, we have the groundwork that could really make graphene take off.”
Reaching higher and higher device density is also important, along with the ability to control the number of layers of graphene produced. The group has demonstrated that in their multilayer graphene, each layer retains the desired properties.
“Multilayer graphene has different stacking than graphite, the material found in pencils,” Conrad noted. “In graphite, every layer is rotated 60 degrees and that’s the only way that nature can do it. When we grow graphene on silicon carbide, the layers are rotated 30 degrees. When that happens, the symmetry of the system changes to make the material behave the way we want it to.”
Epitaxial Versus Exfoliated
Much of the world’s graphene research – including work leading to the Nobel – involved the study of exfoliated graphene: layers of the material removed from a block of graphite, originally with tape. While that technique produces high-quality graphene, it’s not clear how that could be scaled up for industrial production.
While agreeing that the exfoliated material has produced useful information about graphene properties, de Heer dismisses it as “a science project” unlikely to have industrial electronics application.
“Electronics companies are not interested in graphene flakes,” he said. “They need industrial graphene, a material that can be scaled up for high-volume manufacturing. Industry is now getting more and more interested in what we are doing.”
De Heer says Georgia Tech’s place in the new graphene world is to focus on electronic applications.
“We are not really trying to compete with these other groups,” he said. “We are really trying to create a practical electronic material. To do that, we will have to do many things right, including fabricating a scalable material that can be made as large as a wafer. It will have to be uniform and able to be processed using industrial methods.”
Resolving Technical Issues
Among the significant technical issues facing graphene devices has been electron scattering that occurs at the boundaries of nanoribbons. If the edges aren’t perfectly smooth – as usually happens when the material is cut with electronic beams – the roughness bounces electrons around, creating resistance and interference.
To address that problem, de Heer and his team recently developed a new “templated growth” technique for fabricating nanometer-scale graphene devices. The technique involves etching patterns into the silicon carbide surfaces on which epitaxial graphene is grown. The patterns serve as templates directing the growth of graphene structures, allowing the formation of nanoribbons of specific widths without the use of e-beams or other destructive cutting techniques.
Graphene nanoribbons produced with these templates have smooth edges that avoid electron-scattering problems.
“Using this approach, we can make very narrow ribbons of interconnected graphene without the rough edges,” said de Heer. “Anything that can be done to make small structures without having to cut them is going to be useful to the development of graphene electronics because if the edges are too rough, electrons passing through the ribbons scatter against the edges and reduce the desirable properties of graphene.”
In nanometer-scale graphene ribbons, quantum confinement makes the material behave as a semiconductor suitable for creation of electronic devices. But in ribbons a micron or so wide, the material acts as a conductor. Controlling the depth of the silicon carbide template allows the researchers to create these different structures simultaneously, using the same growth process.
“The same material can be either a conductor or a semiconductor depending on its shape,” noted de Heer. “One of the major advantages of graphene electronics is to make the device leads and the semiconducting ribbons from the same material. That’s important to avoid electrical resistance that builds up at junctions between different materials.”
After formation of the nanoribbons, the researchers apply a dielectric material and metal gate to construct field-effect transistors. While successful fabrication of high-quality transistors demonstrates graphene’s viability as an electronic material, de Heer sees them as only the first step in what could be done with the material.
“When we manage to make devices well on the nanoscale, we can then move on to make much smaller and finer structures that will go beyond conventional transistors to open up the possibility for more sophisticated devices that use electrons more like light than particles,” he said. “If we can factor quantum mechanical features into electronics, that is going to open up a lot of new possibilities.”
Collaborations with Other Groups
Before engineers can use epitaxial graphene for the next generation of electronic devices, they will have to understand its unique properties. As part of that process, Georgia Tech researchers are collaborating with scientists at the National Institute of Standards and Technology (NIST). The collaboration has produced new insights into how electrons behave in graphene.
In a recent paper published in the journal Nature Physics, the Georgia Tech-NIST team described for the first time how the orbits of electrons are distributed spatially by magnetic fields applied to layers of epitaxial graphene. They also found that these electron orbits can interact with the substrate on which the graphene is grown, creating energy gaps that affect how electron waves move through the multilayer material.
“The regular pattern of magnetically-induced energy gaps in the graphene surface creates regions where electron transport is not allowed,” said Phillip N. First, a professor in the Georgia Tech School of Physics and MRSEC member. “Electron waves would have to go around these regions, requiring new patterns of electron wave interference. Understanding this interference would be important for some bi-layer graphene devices that have been proposed.”
Earlier NIST collaborations led to improved understanding of graphene electron states, and the way in which low temperature and high magnetic fields can affect energy levels. The researchers also demonstrated that atomic-scale moiré patterns, an interference pattern that appears when two or more graphene layers are overlaid, can be used to measure how sheets of graphene are stacked.
In a collaboration with the U.S. Naval Research Laboratory and University of Illinois at Urbana-Champaign, a group of Georgia Tech professors developed a simple and quick one-step process for creating nanowires on graphene oxide.
“We’ve shown that by locally heating insulating graphene oxide, both the flakes and the epitaxial varieties, with an atomic force microscope tip, we can write nanowires with dimensions down to 12 nanometers,” said Elisa Riedo, an associate professor in the Georgia Tech School of Physics and a MRSEC member. “And we can tune their electronic properties to be up to four orders of magnitude more conductive.”
A New Industrial Revolution?
Though graphene can be grown and fabricated using processes similar to those of silicon, it is not easily compatible with silicon. That means companies adopting it will also have to build new fabrication facilities – an expensive investment. Consequently, de Heer believes industry will be cautious about moving into a new graphene world.
“Silicon technology is completely entrenched and well developed,” he admitted. “We can adopt many of the processes of silicon, but we can’t easily integrate ourselves into silicon. Because of that, we really need a major paradigm shift. But for the massive electronics industry, that will not happen easily or gently.”
He draws an analogy to steamships and passenger trains at the dawn of the aviation age. At some point, it became apparent that airliners were going to replace both ocean liners and trains in providing first-class passenger service. Though the cost of air travel was higher, passengers were willing to pay a premium for greater speed.
“We are going to see a coexistence of technologies for a while, and how the hybridization of graphene and silicon electronics is going to happen remains up in the air,” de Heer predicted. “That is going to take decades, though in the next ten years we are probably going to see real commercial devices that involve graphene.”
Materials Research Science and Engineering Center
In 2008, the National Science Foundation (NSF) awarded an $8 million Materials Research Science and Engineering Center (MRSEC) to a team of universities headed by Georgia Tech. Dennis Hess, a professor in the Georgia Tech School of Chemical and Biomolecular Engineering, directs the center – which is focusing on future electronic materials – with graphene its first target.
“Our goal is to develop both the science and technology, and supply the education, outreach and training needed for the new kinds of scientists and engineers who will work with these new electronic materials,” said Hess. “We want to link all of these things together to create a new platform for integrated circuits.”
Beyond the knowledge of epitaxial graphene for electronics – which was developed at Georgia Tech – the MRSEC will also tap Georgia Tech’s broad experience with microelectronics and nanoelectronics. “It will take both the knowledge of the material and a deep understanding of the electronics to make this work,” he added.