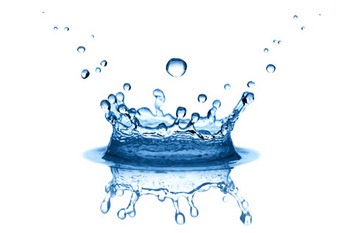
Providing a possible new route to hydrogen-gas production, researchers at the California Institute of Technology (Caltech) have devised a series of chemical reactions that allows them, for the first time, to split water in a nontoxic, noncorrosive way, at relatively low temperatures.
A research group led by Mark Davis, the Warren and Katharine Schlinger Professor of Chemical Engineering at Caltech, describes the new, four-reaction process in the early edition of the Proceedings of the National Academy of Sciences(PNAS).
Hydrogen is a coveted gas: industry uses it for everything from removing sulfur from crude oil to manufacturing vitamins. Since its combustion does not emit carbon dioxide into the atmosphere, there is some belief that it could even fuel a potential “hydrogen economy”—an energy-delivery system based entirely on this one gas. But since there is no abundant supply of hydrogen gas that can be simply tapped into, this lighter-than-air gas has to be mass-produced.
One way to make hydrogen is by using heat to split water, yielding pure hydrogen and oxygen. Known as thermochemical water splitting, this method is appealing because it can take advantage of excess heat given off by other processes. Thus far, it has been attempted in two ways: using two steps and taking advantage of high temperatures (above 1000°C) associated with solar collectors; or through multiple steps at “lower temperatures”—those below 1000°C—where, for example, the excess heat from nuclear reactors could drive the chemistry.
Davis is interested in this latter approach, which actually takes him back to his academic roots: his first paper as a graduate student dealt with a low-temperature water-splitting cycle, called the sulfur-iodine system, which has since been piloted for use around the world. Although that cycle operates at a maximum temperature of 850°C, it also produces a number of toxic and corrosive liquid intermediates that have to be dealt with. The cycle’s high-temperature counterparts typically involve simpler reactions and solid intermediates—but there are very few processes that produce excess heat at such high temperatures.
“We wanted to combine the best of both worlds,” Davis says. “We wanted to use solids, as they do in the high-temperature cycles, so we could avoid these toxicity and corrosion issues. But we also wanted to learn how to lower the temperature.”
The first thing postdoctoral scholar and lead author Bingjun Xu and graduate student Yashodhan Bhawe did was to prove via thermodynamic arguments that a two-step, low-temperature cycle for water splitting will not be practical. “Nature’s telling you ‘No way,'” Davis says. “It was really a key point that told us we had to go away from looking for a two-step process, and that guidance directed us down another pathway that turned out to be quite fruitful.”
The four-reaction cycle the team came up with begins with a manganese oxide and sodium carbonate, and is a completely closed system: the water that enters the system in the second step comes out completely converted into hydrogen and oxygen during each cycle. That’s important because it means that none of the hydrogen or oxygen is lost, and the cycle can run over and over, splitting water into the two gases. In the current paper, the researchers ran their newly created cycle five times to show reproducibility. It will be needed to show that the cycle can run thousands of times in order to be practical. Experiments of this type are beyond the capabilities currently in the Davis lab.
“We’re excited about this new cycle because the chemistry works, and it allows you to do real thermochemical water splitting with temperatures of 850°C without producing any of the halides or other types of corrosive acids that have been problems in the past,” Davis says. Still, he is careful to point out that the implementation of the cycle as a functioning water-splitting system will require clever engineering. For example, for practical purposes, engineers will want some of the reactions to go faster, and they would also need to build processing reactors that have efficient-energy flows and recycling amongst the different stages of the cycle.
Going forward, the team plans to study further the chemistry of the cycle at the molecular level. They have already learned that shuttling sodium in and out of the manganese oxide is critical in lowering the operating temperature, but they want to know more about what exactly is happening during those steps. They hope that the enhanced understanding will allow them to devise cycles that could operate at even lower maximum temperatures.
Figuring out ways to decrease the operating temperatures is at the heart of Davis’s interest in this project. “What we’re trying to ask is, ‘Where are the places around the world where people are just throwing away energy in the form of heat?'” he says. He speculates that there could be a day when water-splitting plants are able to run on the heat given off by a variety of manufacturing industries such as the steel- and aluminum-making industries and the petrochemicals industries, and by the more traditional power-generation industries. “The lower the temperature that we can use for driving these types of water-splitting processes,” he says, “the more we can make use of energy that people are currently just wasting.”
The PNAS paper, “Low-temperature, manganese oxide-based thermochemical water splitting cycle” is now online. The work was funded by a donation from Mr. and Mrs. Lewis W. van Amerongen.