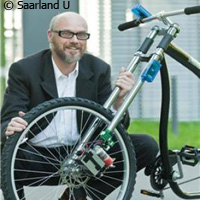
Europeans support and drive innovation; a recent addition to this trend is a wireless bicycle brake developed by computer scientists at Saarland University in Germany.
Demonstrating the wireless bicycle brake system’s efficiency on a ‘cruiser bike’, the team validated the system’s reliability using mathematical calculations that are also used for aircraft or chemical function control systems. According to the scientists, the safety rate reached for this system is just short of 100%.
Unlike a conventional bike, the team compares the cruiser bike to that of an Easy Rider motorcycle without an engine block. What sets this latest system apart, however, is the lack of a protruding brake lever to control the front brake. It also does not have a brake cable snaking down the frame. This wireless bicycle brake is something more than just a gadget, they say.
‘Wireless networks are never a fail-safe method. That’s a fact that’s based on a technological background,’ comments Professor Holger Hermanns of Saarland University , who developed the wireless bicycle brake system in cooperation with his team. But what interests scientists most is developing wireless systems with non-stop functioning features, just like a typical bicycle brake.
‘In the field of the future European Train Service, for example, concrete plans already exist,’ Professor Hermanns says. ‘Train and airplane experiments are far too sophisticated, and could even endanger the life of human beings in case of malfunction.’
So the mathematical methods performed by the Saarland team should substantiate the correct function and interaction of the components automatically.
‘The wireless bicycle brake gives us the necessary playground to optimize these methods for operation in much more complex systems,’ explains Professor Hermanns. The scientists thus chose to investigate the brake prototype with algorithms that are usually used in control systems for aircraft or chemical factories. The outcome? A wireless bicycle brake that works with 99.999999999997% reliability.
‘This implies that out of a trillion braking attempts, we have three failures,’ Professor Hermanns remarks, adding: ‘That is not perfect, but acceptable.’
A user must clench the rubber grip on the right handle in order to bring the bike to a full stop. The more tightly the grip is clenched, the harder the disk brake on the front wheel works. Several electronic components activate the braking system. The rubber grip is equipped with a pressure sensor that activates a sender if a specified pressure threshold is crossed, the team says. The sender is found within a blue plastic box whose size is similar to that of a pack of cigarettes and is attached to the handlebar.
The radio signals are sent to a receiver attached at the end of the bicycle’s fork. The receiver forwards the signal to an actuator, converting the radio signal into the mechanical power that kick-starts the disk brake. Extra senders are attached to the bicycle so as to give reliability a boost. These repeatedly send the same signal.
A cruiser bike can brake within 250 milliseconds, based on the existing configuration. So a cyclist must react 2 meters before reaching a risky situation if they are cycling at a speed of 30 kilometers per hour. However, this functionality needs a boost, according to the researchers.
Says Professor Hermanns: ‘It is not difficult to integrate an anti-lock braking system and traction control. That takes only a few adjustments.’